Nawiedzony pokój, ręce robota i ściana pełna światła. Zobaczyłem, jak powstaje mój smart dom
20 minut jazdy taksówką od poznańskiego dworca, w budynkach, które ledwo widać z głównej drogi, prawdopodobnie już dziś wiedzą, jak będą wyglądać i działać nasze domy za kilka lub kilkanaście lat. I kilkadziesiąt metrów dalej pewnie już szykują produkcję urządzeń, które w tych domach się znajdą.
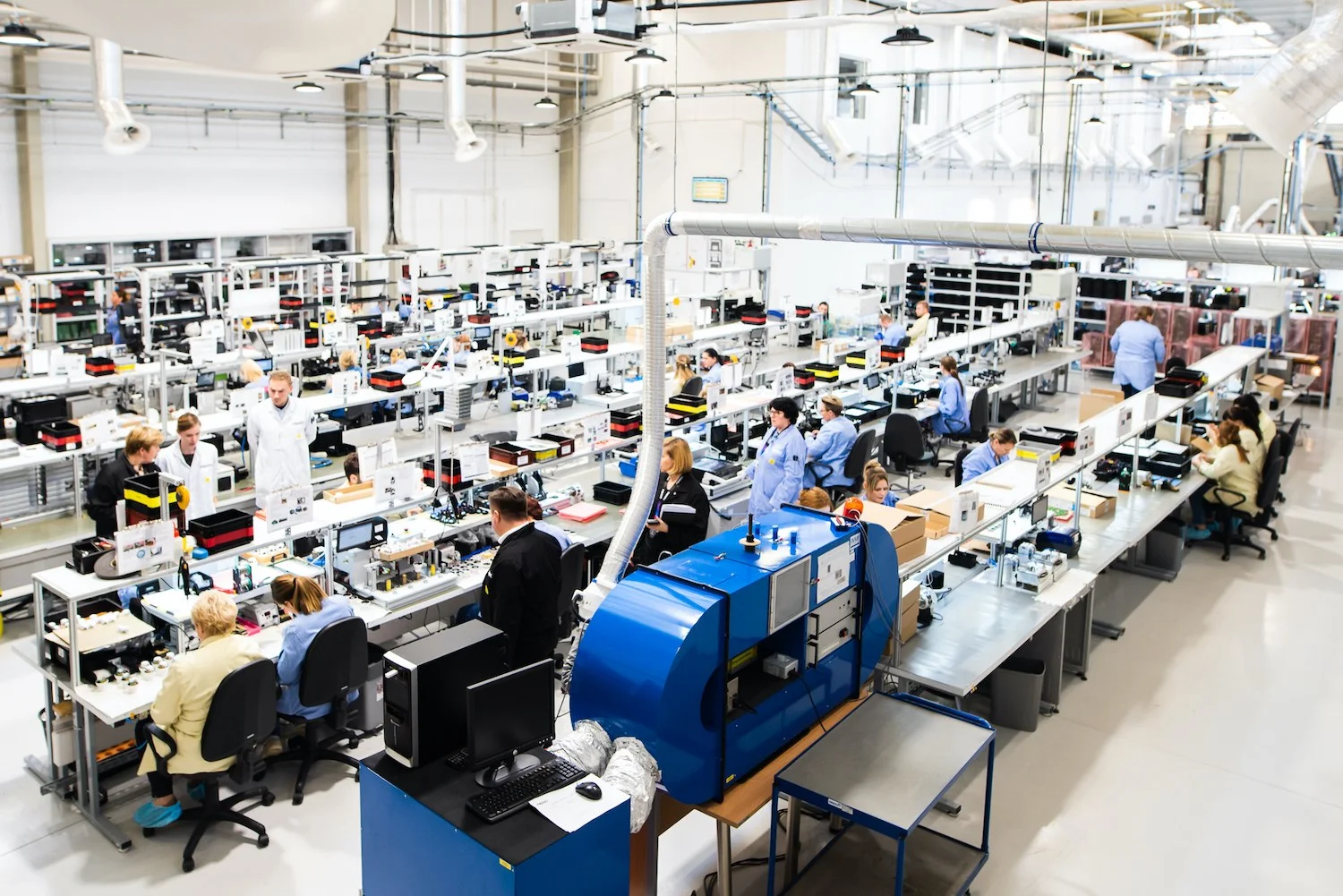
Wysogotowo - niewielka wieś pod Poznaniem, oddzielona od stolicy województwa szerokim i gęstym lasem. Mniej niż 1000 mieszkańców, salon samochodowy, radar meteorologiczny, kilka ulic na krzyż i to już koniec. Rowerem dałoby się przejechać przez całą miejscowość w kilka minut. Jadąc autem, pewnie nawet nie zarejestrowalibyśmy faktu przejechania przez tę wieś, zlewającą się w trasie ze wszystkimi innymi, niewiele znaczącymi zabudowaniami.
Jeśli jednak zwolnimy i skręcimy w jedną z bocznych uliczek, trafimy do miejsca, gdzie robotyczne ręce godzinami sprawdzają wytrzymałość specjalnych przycisków, okna co jakiś czas otwierają się i zamykają same, a kaloryfery samodzielnie uznają, czy warto trochę podkręcić temperaturę, czy może już wystarczy. I miejsca, gdzie inżynierowie regularnie - z obowiązku, ale pewnie też trochę w ramach rozrywki - sprawdzają, jak mocno trzeba przeciążyć dany moduł, żeby zostawił na tablicy przysmolony ślad.
Wreszcie miejsca, z którego każdego roku w świat wychodzić będą aż cztery miliony urządzeń do obsługi smart domów. W tym - być może - i do mojego. Ale to temat na inną opowieść.
Witajcie w nowej fabryce Fibaro.
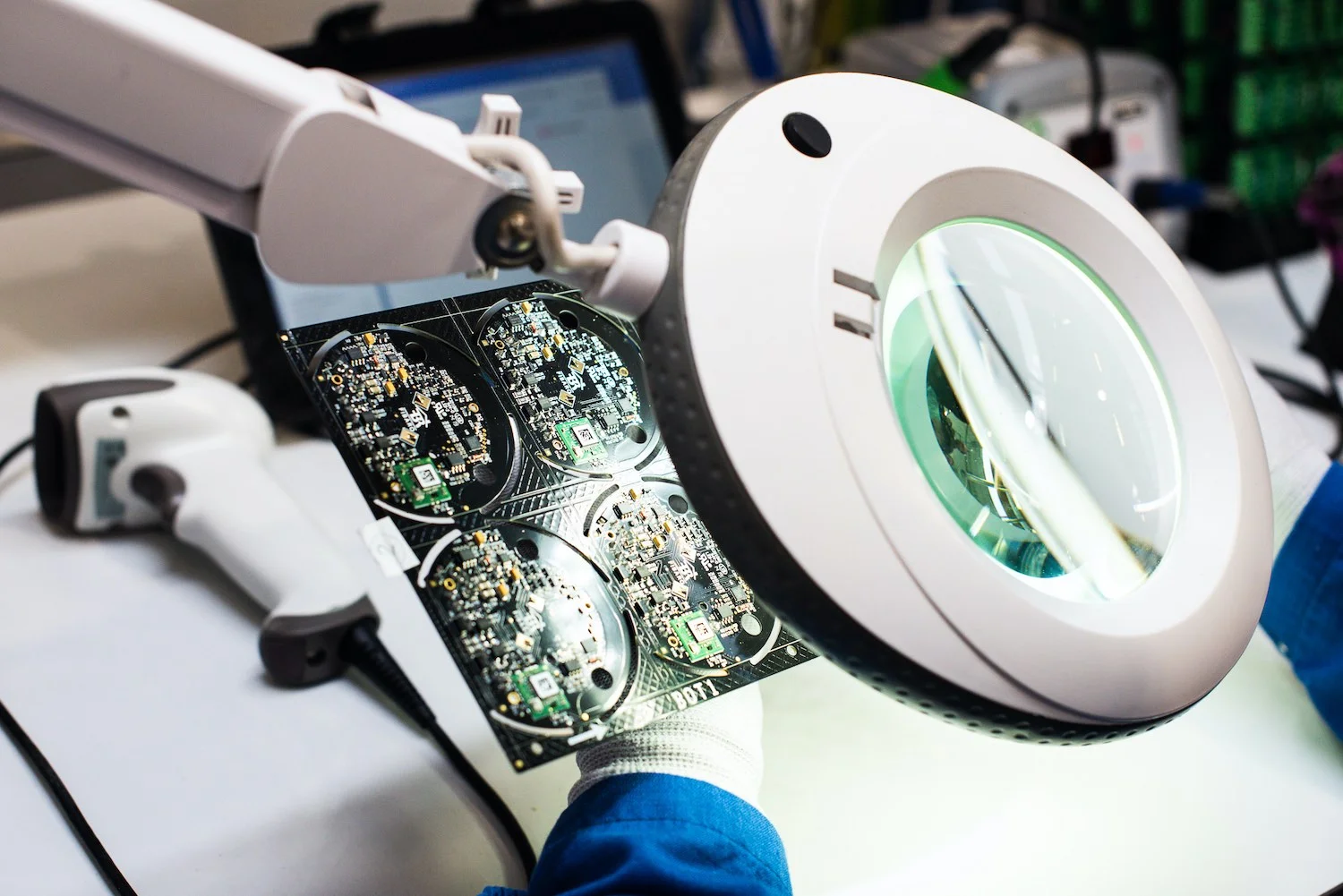
A może raczej - w centrum Fibaro. Bo pod Poznaniem znajduje się nie tylko otwarta w połowie tego roku fabryka, zajmująca powierzchnię ok. 4000 m2 (z czego 1200 m2 to powierzchnia produkcyjna), ale też centrum R&D i główna siedziba firmy. W jednym miejscu, na względnie niewielkiej przestrzeni, skupiony jest więc cały proces - od fazy zupełnie abstrakcyjnego pomysłu, przez próby jego technicznej realizacji i projektowania, po testy i dalszą produkcję oraz weryfikację jakości.
Nic dziwnego, że firma ani nie produkuje swojego sprzętu poza granicami Polski, ani też nie zamierza wydzielić działu produkcyjnego np. do Chin czy na Tajwan. Może i byłoby to tańsze rozwiazanie, ale zdecydowanie opóźniłoby cały proces, a do tego potencjalnie utrudniło kontrolę jakości. A jedno i drugie - szczególnie w tak szybko rozwijającej się branży - mogłoby być opłakane w skutkach.
Żeby było ciekawiej, spora część materiałów wykorzystywanych przez Fibaro pochodzi od lokalnych dostawców. Z elektroniką nie jest wprawdzie aż tak łatwo, ale przykładowo tworzywa do konstrukcji obudów czy kartony z nadrukami do pakowania pochodzą z zakładów znajdujących się na terenie Polski.
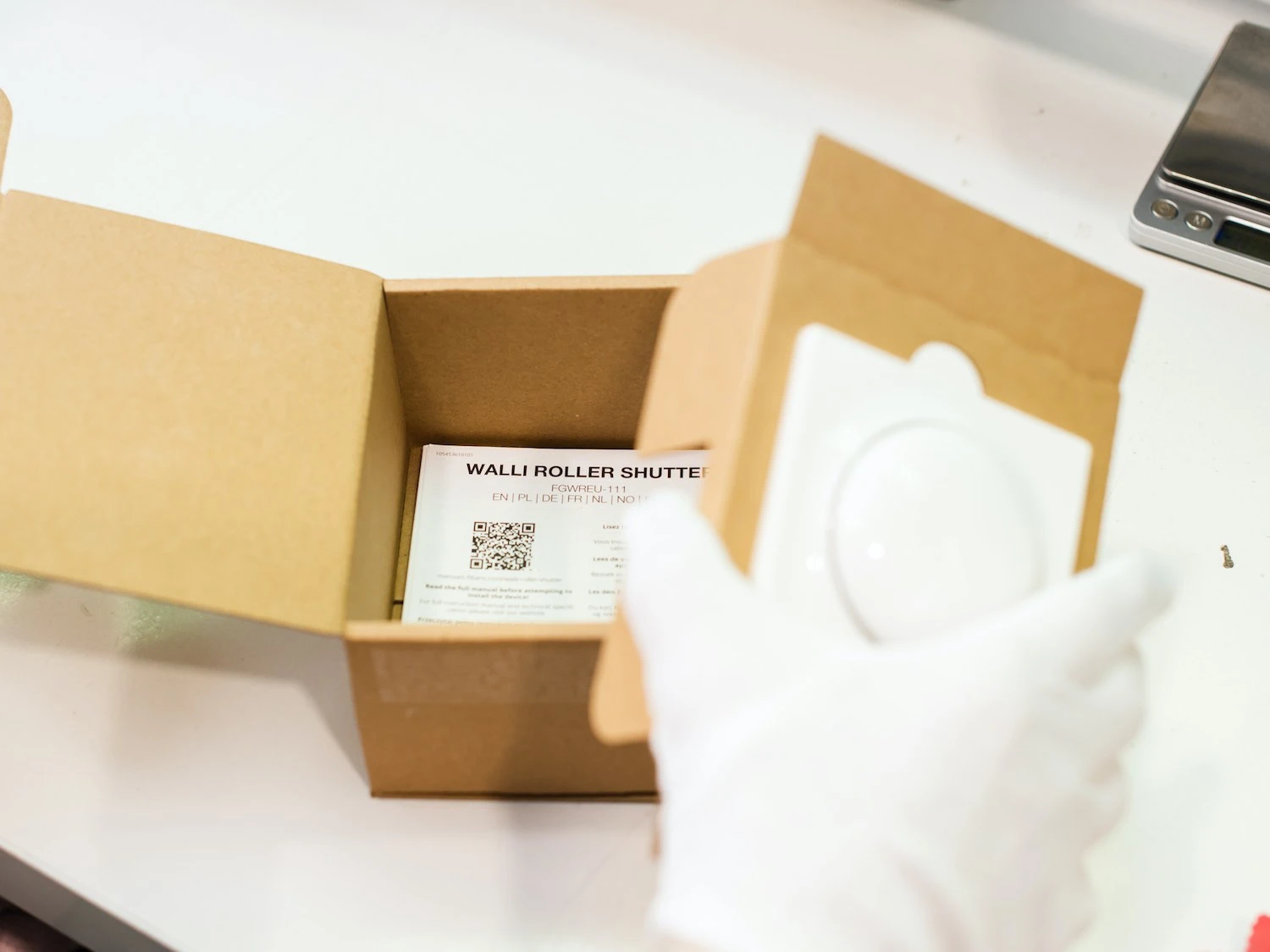
Coś jednak innego już od początku zwraca moją uwagę.
A jest tym fakt, że firma... sama wierzy w swoje produkty. W części biurowej - od holu, aż po poszczególne pomieszczenia służbowe - rzadko kiedy uświadczymy analogowe przełączniki - przeważnie zastępują je dużo bardziej efektowne i funkcjonalne przełączniki z serii Walli. Na grzejnikach dumnie zatknięte pracują głowice termostatyczne Fibaro. Przy przełącznikach rolet połyskuje charakterystyczny, podświetlany pierścień. Tu i ówdzie - chociażby na ladzie w recepcji - parami lub samotnie leżą rozstawione Buttony.
Nie wiem dokładnie, ile urządzeń Fibaro pracuje w całym budynku - cały czas zresztą dokładane są nowe, bo firma przeprowadziła się do tej lokalizacji dopiero niedawno. Wiem jednak, że jest ich tak wiele, że niezbędne było wykorzystanie co najmniej kilku - jeśli nie większej liczby - centralek. Mamy więc do czynienia z całkiem ciekawym przypadkiem - firma właściwie sama na sobie testuje działanie tworzonego przez siebie systemu, do tego w mocno skomplikowanych i wymagających warunkach.
Tak - bez wątpienia to w pewnej mierze pokazówka, ale mnie przekonuje.
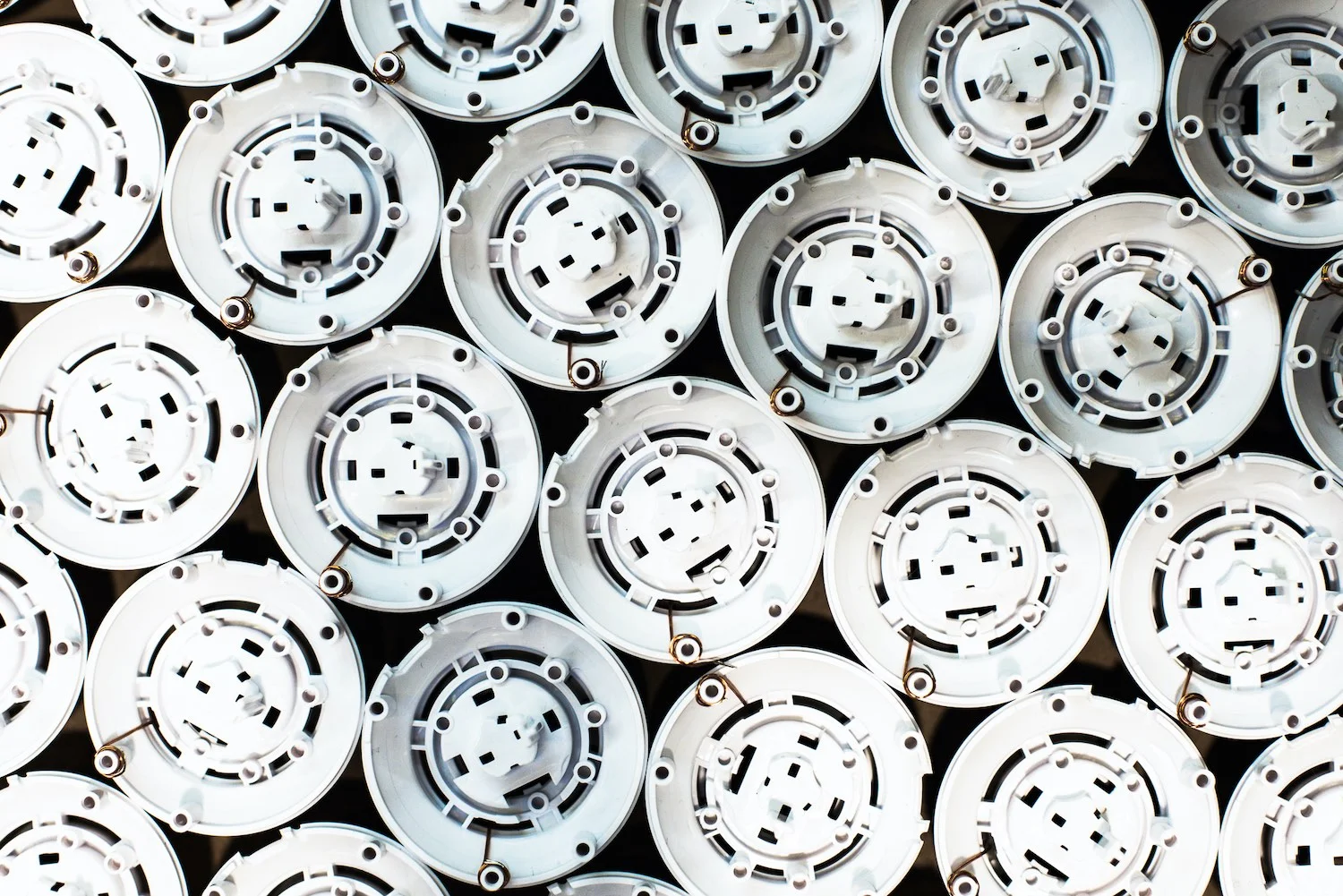
Tym bardziej, że - czemu akurat trudno się dziwić - żywy organizm siedziby Fibaro to nie jedyne miejsce, gdzie testuje się produkty tej marki. Za - w większości - zamkniętymi drzwiami licznych laboratoriów od rana do wieczora trwają testy, uwzględniające różne sytuacje i różne tematy testowe.
Nie ma szans, żebym dostał się do każdego z nich. W niektórych pewnie już teraz testowane są sprzęty, które dopiero co wejdą do produkcji i jeszcze nie zostały zapowiedziane. W tych, do których mnie jednak dopuszczono, nie sposób się nudzić. Tu sprawdzana jest w specjalnej komorze wytrzymałość urządzenia na zewnętrzne warunki atmosferyczne. Tutaj robotyczne ręce wciskają Buttona bez przerwy przez cały dzień, żeby sprawdzić, kiedy nadejdzie jego fizyczny kres. W jeszcze innym pomieszczeniu przypalona tablica z puszkami elektrycznymi przypomina, że nie każdy pomysł jest dobry. W pomieszczeniu obok znajduje się... dodatkowe pomieszczenie, gdzie na powierzchni niewiele większej niż schowek na miotły ustawiono drukarkę 3D, pozwalającą na szybko przygotowywać kolejne prototypy. Jeszcze gdzie indziej maksymalnie obciąża się kolejne moduły - w tym i konkurencji - sprawdzając, czy - albo i kiedy - będą sprawiały problemy.
Są nawet osobne pomieszczenia, które udają domy lub poszczególne kamery. Samoczynnie, a raczej na zdalne polecenia, otwierają się w nich okna, temperatura wędruje w górę i w dół, zamki otwierają się i zamykają, rolety opuszczają i podnoszą, a gigantyczne klastry żarówek rozświetlają się i gasną. W niektórych pomieszczeniach testowych nawet nikogo nie ma - sterowanie jest zdalne, więc i obserwacje, z wykorzystaniem sprytnie rozmieszczonych kamer, są całkowicie zdalne. W końcu co to za smart dom, jeśli do jego testowania trzeba byłoby wstawać z fotela i łazić po całej firmie.
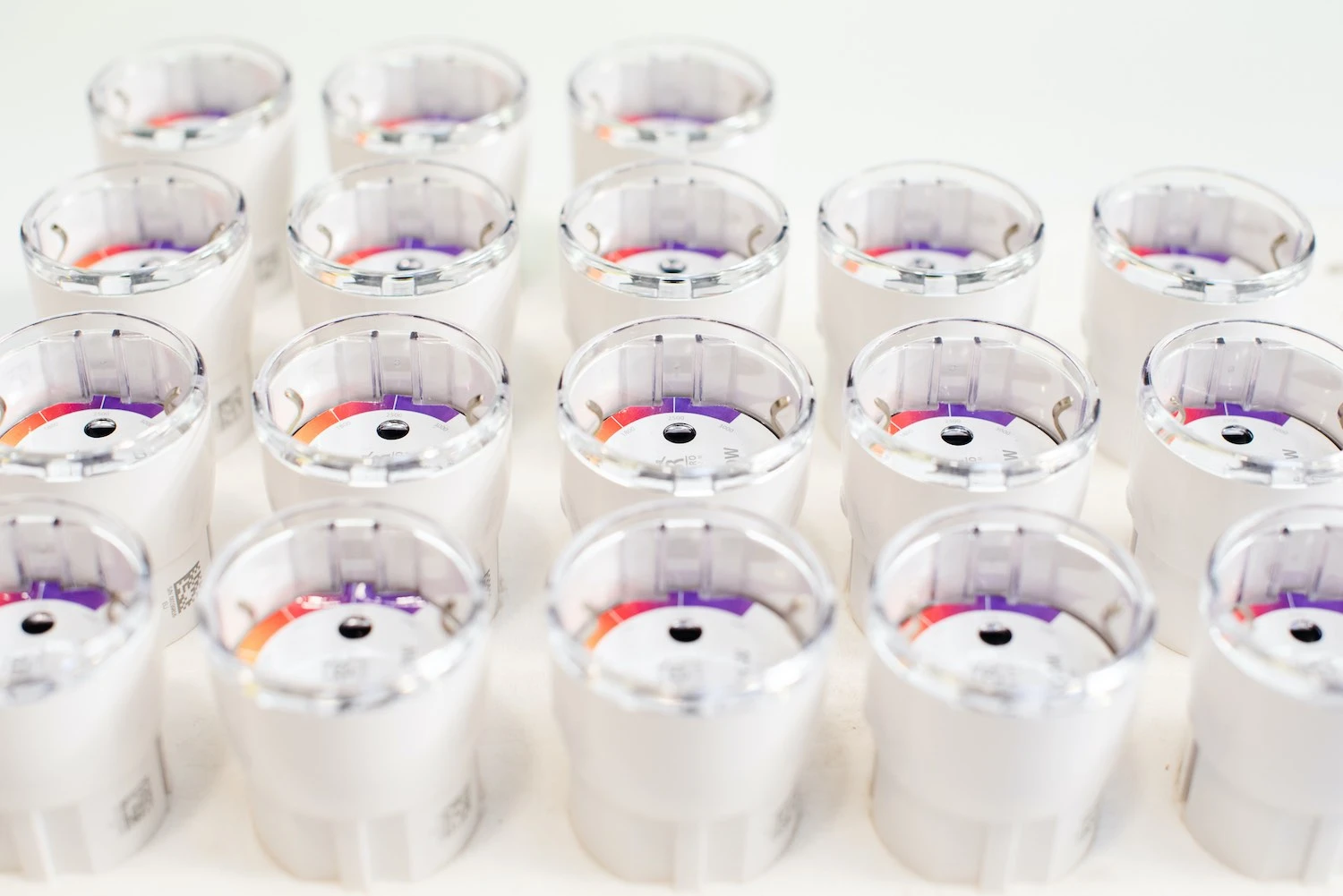
Ja jednak... muszę łazić.
Bo przeglądanie części R&D było tylko niewielkim fragmentem całej wycieczki - choć przyznaję, na poznawanie designerskiej historii produktów, z których korzystam na co dzień, chętnie poświęciłbym jeszcze co najmniej kilka godzin.
Nie ma jednak na to czasu, bo przyjechałem tutaj głównie po to, żeby zobaczyć, jak powstają produkty Fibaro na ostatnim etapie. To jest - w samej fabryce, z której firma jest niesamowicie dumna.
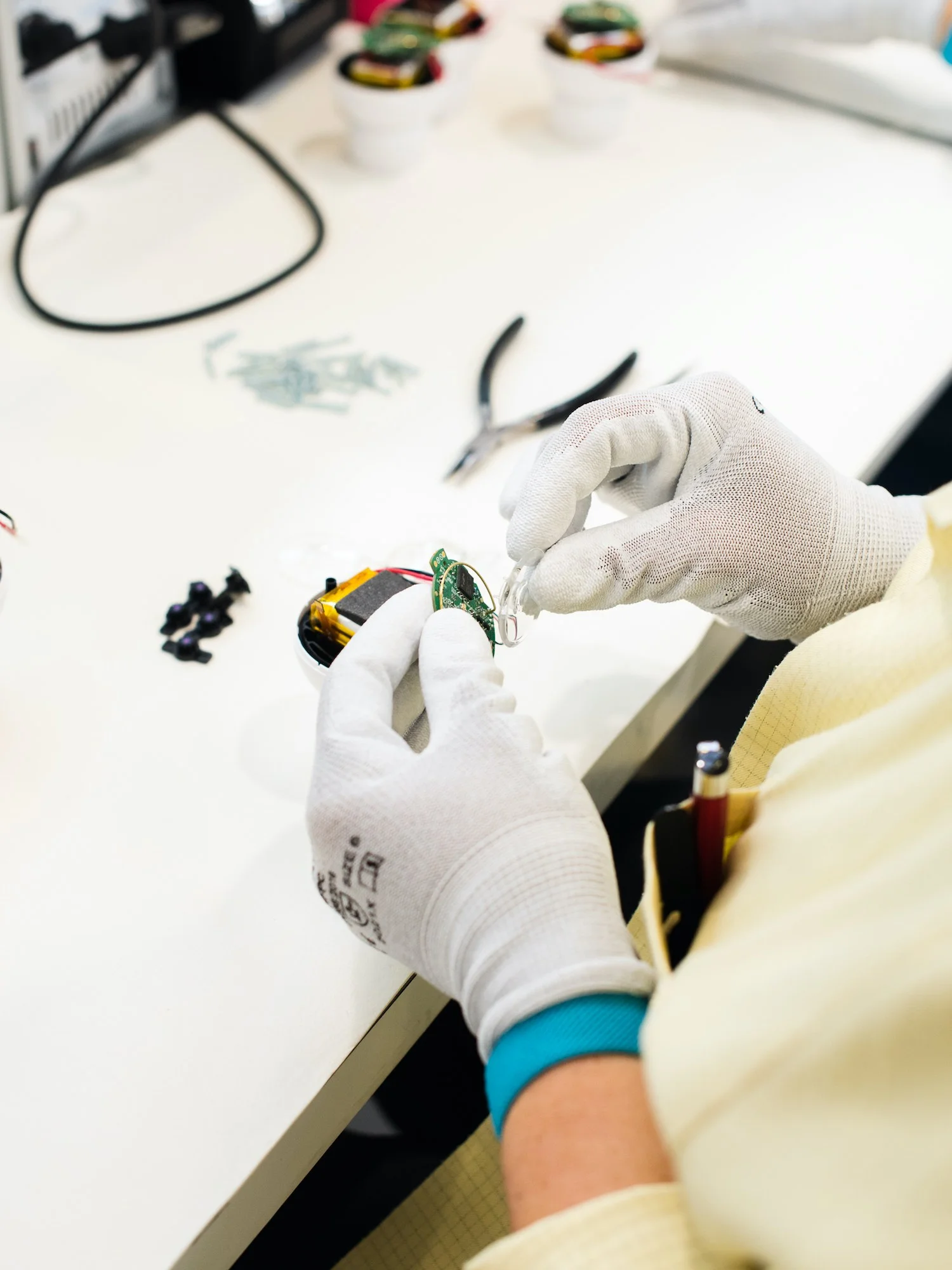
I trudno się temu dziwić. Powierzchnia fabryki jest naprawdę spora, pracuje tu ponad 150 osób, a niektóre rozwiązania i urządzenia były pierwsze/największe (albo jedno i drugie) w tej części Europy (jak na przykład 13-strefowy piec konwekcyjny do lutowania rozpływowego o długości ponad 7 m).Dodatkowo dumą może napawać Fibaro fakt, że części wyprodukowane właśnie w niewielkiej wsi pod Poznaniem, trafiają do kilkudziesięciu krajów na sześciu kontynentach.
Uwagę zwraca przy okazji fakt, jak wiele procesów przy produkcji udało się zautomatyzować, jednocześnie pozostawiając na tyle dużo czynnika ludzkiego, żeby zminimalizować prawdopodobieństwo produkcji wadliwego modułu. I tak np. po początkowej fazie produkcji, gdzie najdrobniejsze elementy montowane są na płytach PCB, następuje kontrola jakości zarówno zautomatyzowana, jak i ludzka. Dopiero potem urządzenie trafia do dalszej produkcji, pod koniec której również jest sprawdzane pod względem funkcjonalnym. Zresztą także na etapie ludzkiego montażu każda część jest dokładnie sprawdzana - również pod kątem wizualnym.
Niedziałające lub wadliwe sprzęty i elementy trafiają natomiast błyskawicznie do odpowiednich działów. Te podejmują się prób ich naprawienia - jeśli się powiedzie, elementy wracają na linie produkcyjne. Jeśli nie - zmierzają do utylizacji.
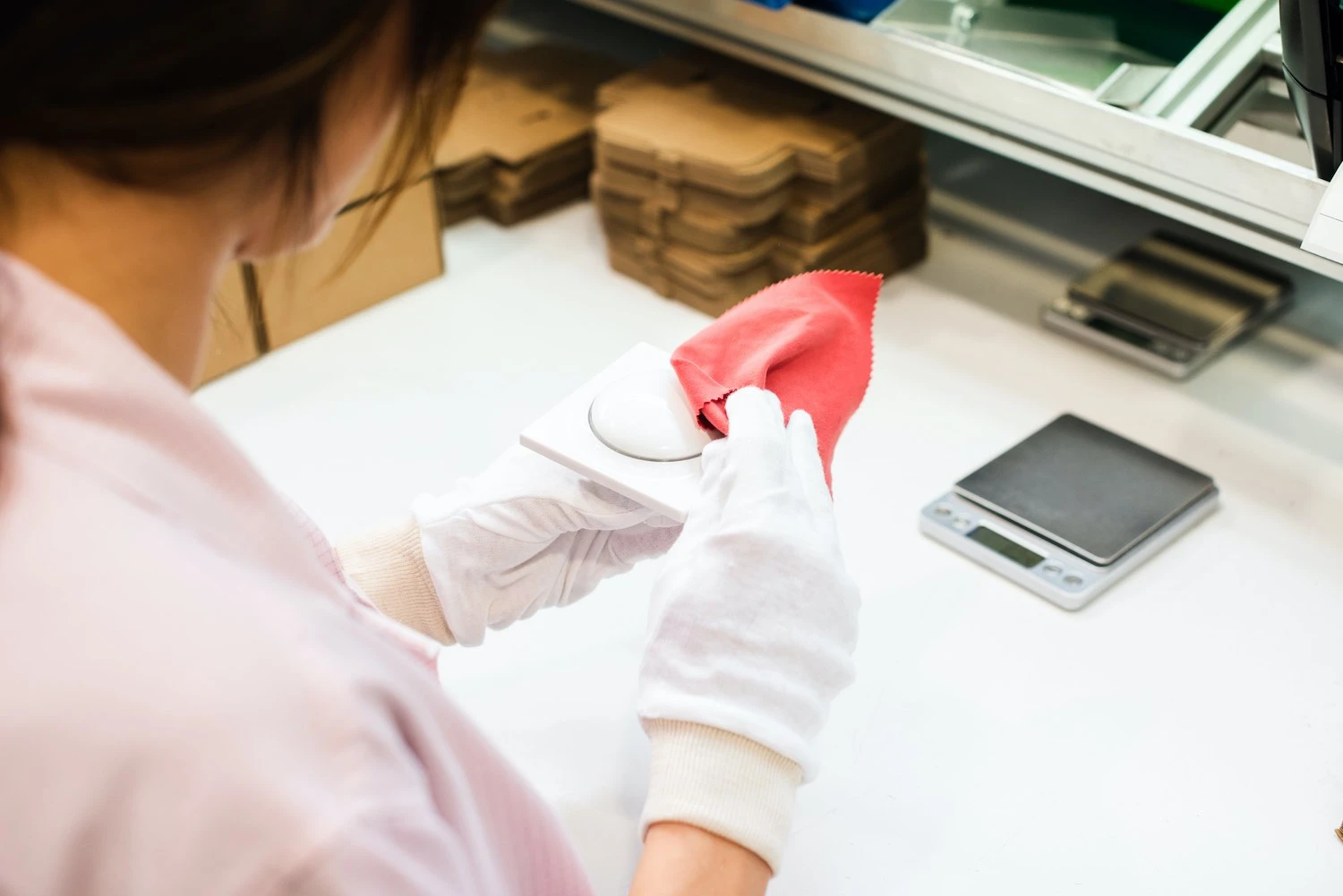
Ludzka weryfikacja i umiejętności to oczywiście nie jedyny powód, dla którego w fabryce Fibaro nie pracują same roboty. Automatyzacja niektórych zadań byłaby... po prostu nieopłacalna. Panuje tu bowiem - w zależności od dnia, tygodnia i zamówień - spora rotacja, jeśli chodzi o produkty montowane na poszczególnych stanowiskach. Nawet w obrębie jednego dnia może się zdarzyć, że pracownik rano składa np. Buttony, a po przerwie obiadowej siada do czujników zalania. Zapobiega to znużeniu i znudzeniu, co jest dość istotne, szczególnie że linia produkcyjna Fibaro jest tak usystematyzowana, podzielona i zorganizowana, że łatwo byłoby popaść w monotonię, robiąc cały czas ten sam fragment.
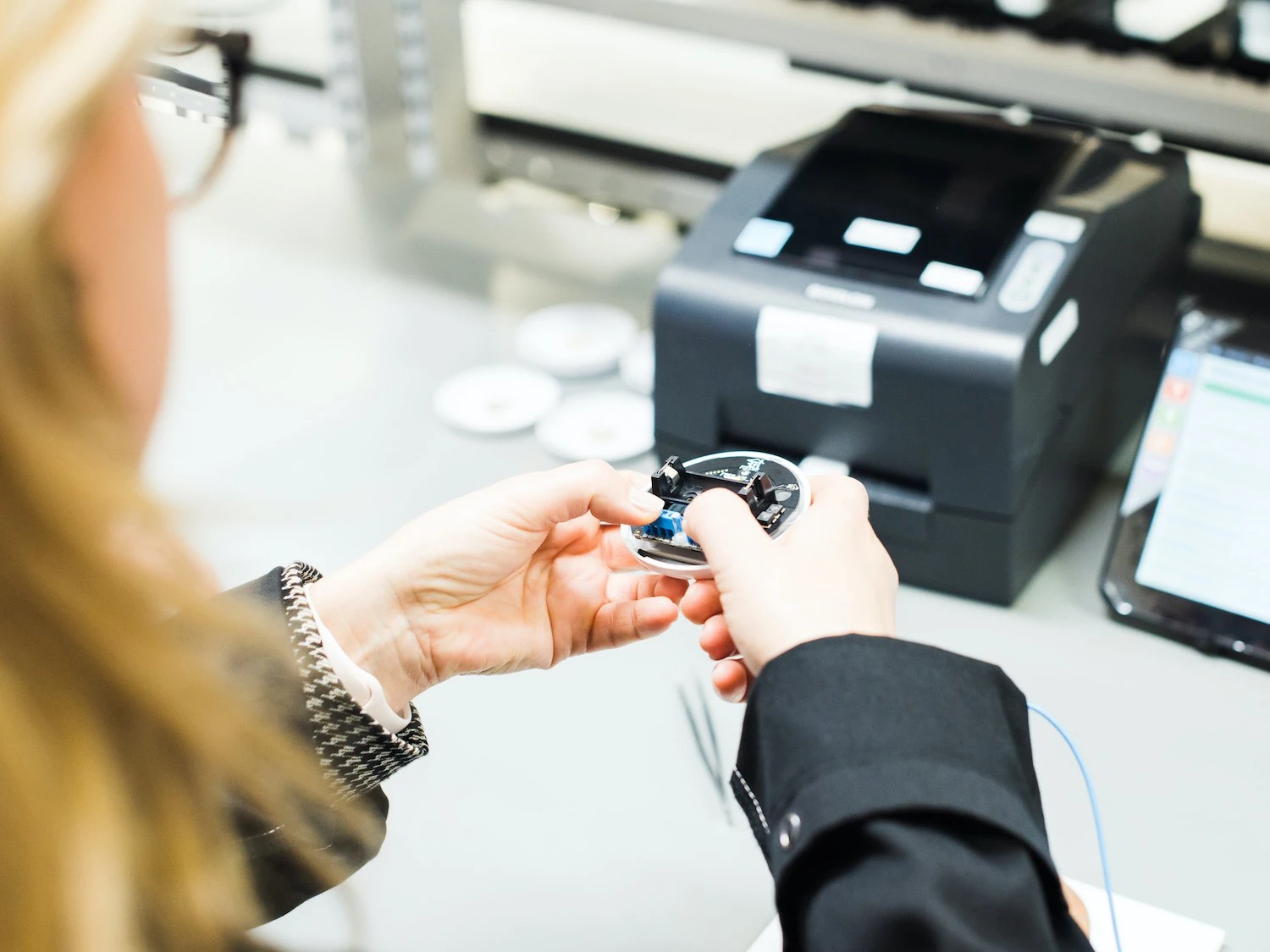
I - żeby nie było żadnych wątpliwości - to wcale nie jest łatwa robota.
Nie miałem wprawdzie okazji samodzielnie się o tym przekonać, ale zrobiło to kilku z dziennikarzy, którzy byli razem ze mną na wycieczce. I choć na pozór wydaje się to wszystko banalnym zadaniem - w końcu trzeba tylko zgodnie z instrukcją połączyć ze sobą kilka gotowych elementów - to jednak... nie wyszło to przesadnie dobrze. Nic dziwnego, że w fabryce Fibaro zatrudnienie często znajdują osoby zajmujące się wcześniej m.in. zegarmistrzostwem. To precyzyjna robota - jeśli nie zostanie precyzyjnie wykonana, może nie przejść testów jakości. A wtedy czas poświęcony na wszystkie wcześniejsze etapy będzie czasem straconym.
Ludzie potrzebni są też w - tak, zgadliście - przeprowadzaniu dodatkowych testów. Przykładowo osobno testowane i certyfikowane są czujniki CO. Sprawdzana jest też skuteczność czujników dymu. Ktoś musi też projektować coraz to nowe urządzenia do zautomatyzowanych testów kolejnych urządzeń na różnych etapach i produktów. Fibaro podaje przy tym, że sporo udogodnień zostało wprowadzonych na wniosek - a czasem i na konkretny pomysł - pracowników fabryki. W końcu to oni najlepiej wiedzą, jak można poprawić komfort czy wydajność pracy. Zastąpienie wszystkiego maszynami raczej nie dałoby takich efektów.
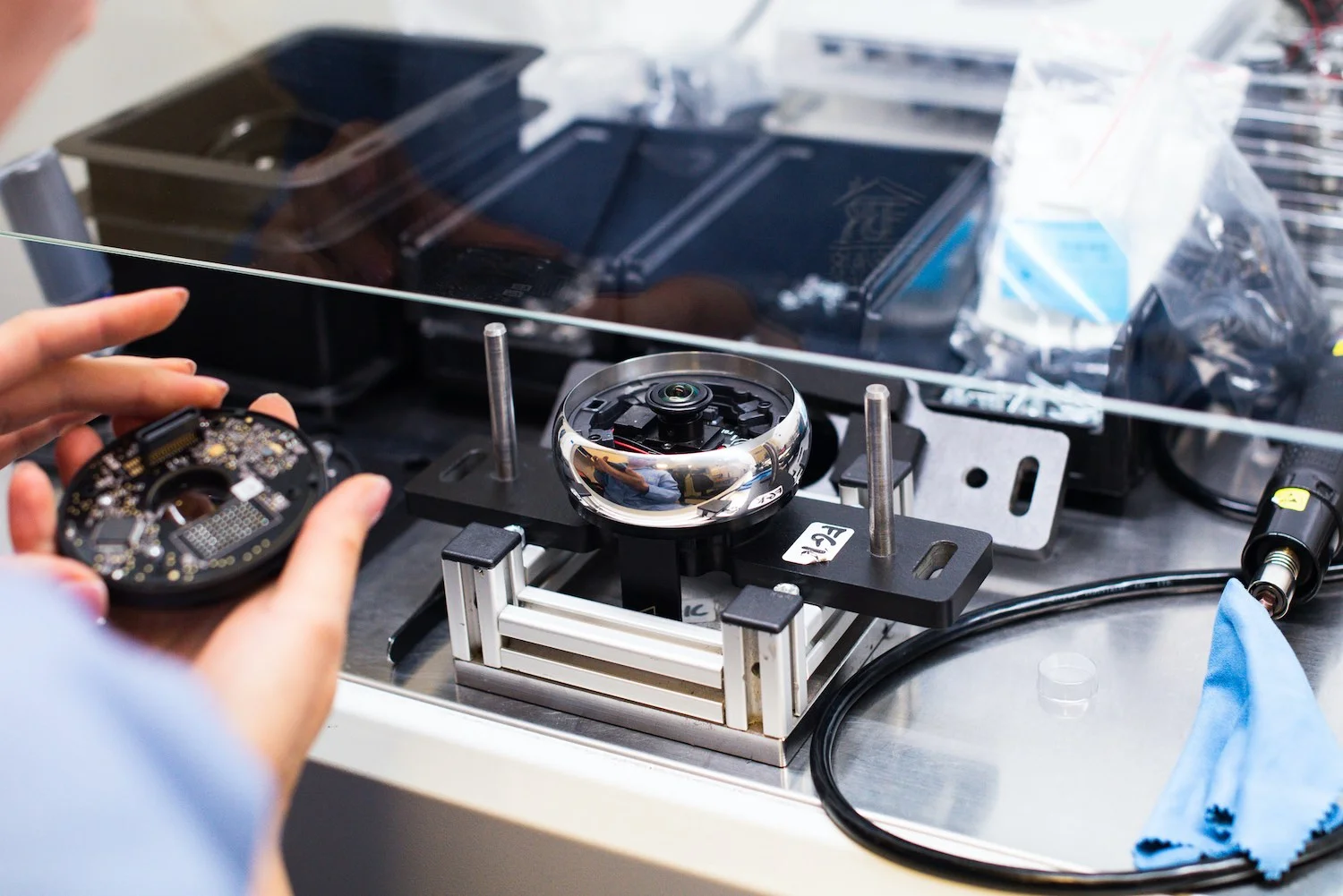
I tak - można odnieść wrażenie, że każdy element jest tutaj testowany kilka razy - zarówno w momencie, kiedy jest jeszcze kupką części, jak i wtedy, kiedy jest już gotowym modułem. I tak - przynajmniej według deklaracji firmy - jest. Wszystkie sprzęty, które wyjeżdżają z podpoznańskiej fabryki, są weryfikowane i testowane. 100 procent.
A jak to się ma do praktyki?
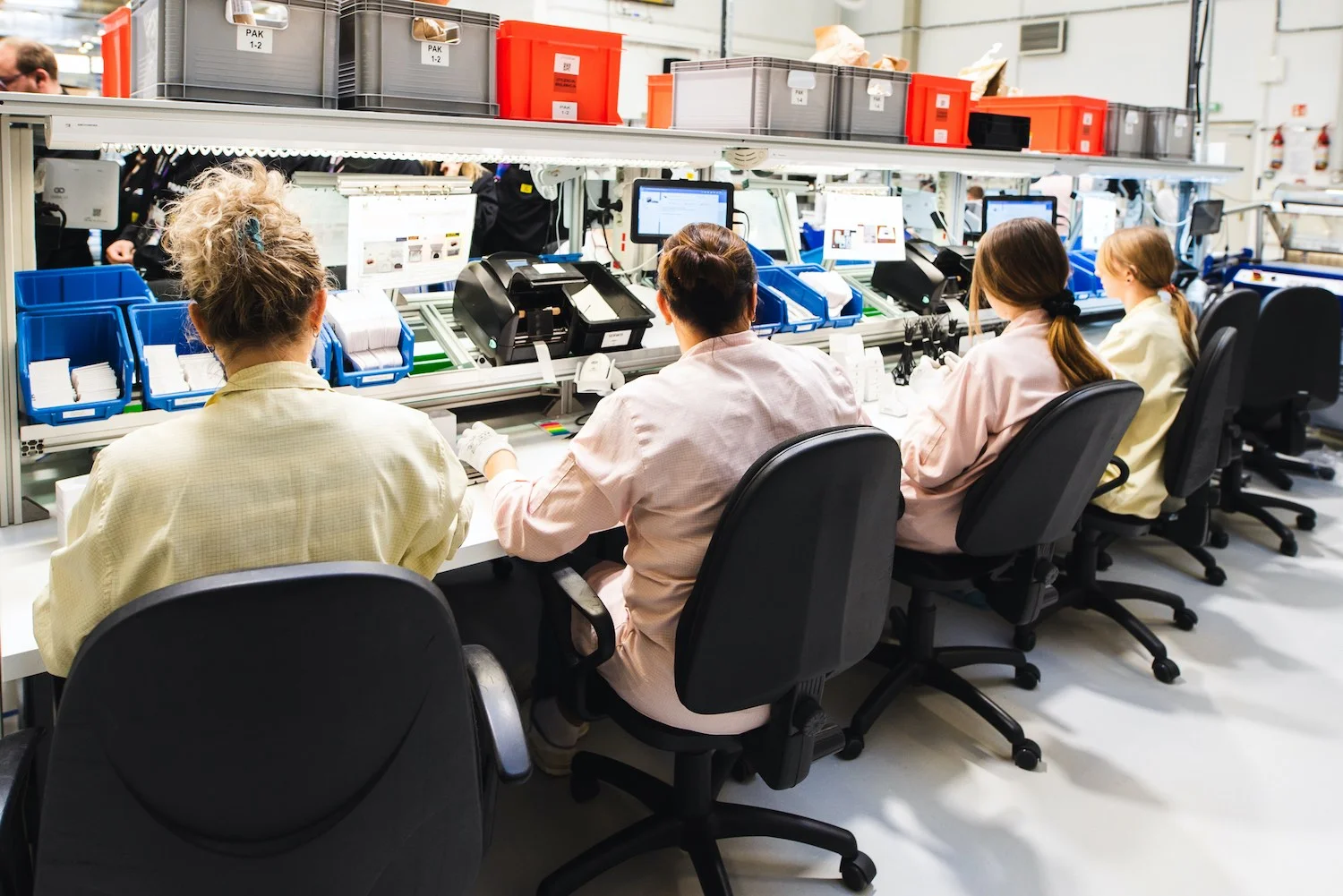
O tym opowiem wam już niedługo, a póki co nie będę jeszcze zdradzał moich pierwszych wniosków i obserwacji. Mogę natomiast napisać co innego - przyjemnie zasypia się w takim smart domu ze świadomością, że komponenty do niego powstały zaledwie 2 godziny jazdy samochodem od niego...