Widziałem, jak Samsung tworzy ekrany LED w cenie mieszkania. Teraz jeszcze bardziej je chcę
Samsung zaprosił mnie do swojej fabryki mieszczącej się w Galancie na Słowacji. Widziałem tam jak wygląda proces produkcji ekranów Micro LED i wam o nim opowiem.
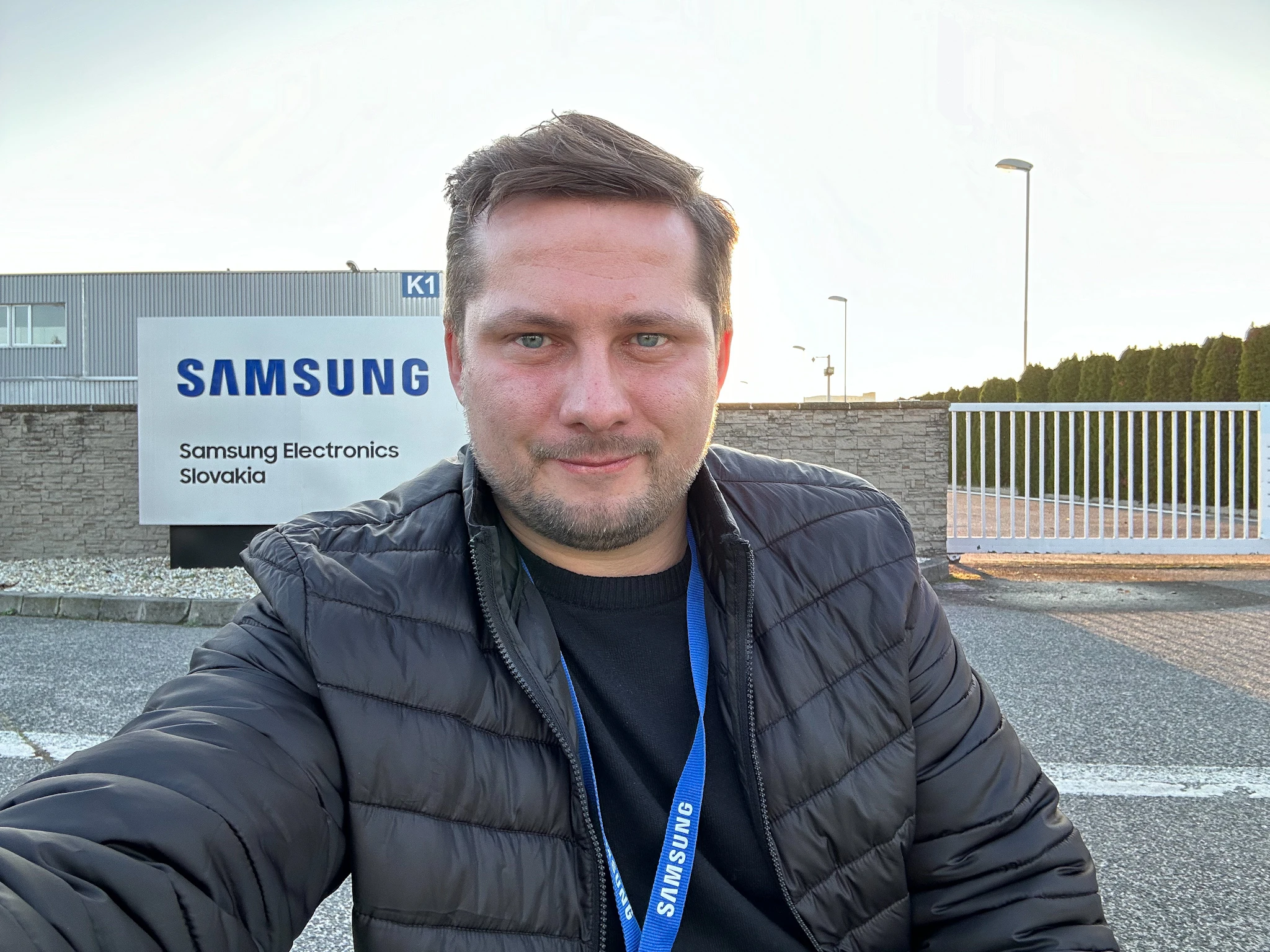
Galanta to miejscowość leżąca kilkadziesiąt kilometrów od Bratysławy. Zamieszkuje ją 15 tysięcy mieszkańców, ale podobnie jak większość takich miasteczek, nigdy nie zaistniała w zbiorowej świadomości. Jednak jeżeli w ostatnich latach kupiliście telewizor marki Samsung, to jest duże prawdopodobieństwo, że pochodzi właśnie stamtąd. To jedna z dwóch europejskich fabryk, w których powstają telewizory producenta. Druga mieści się na Węgrzech, ale nie jest tak wyjątkowa jak ta słowacka, gdzie istnieją dwie oddzielne hale, w których powstają tak różne produkty. W pierwszej, w której nie byłem, produkuje się konwencjonalne telewizory z każdej serii produktowej Samsunga. Pracuje tam ponad tysiąc osób, a jeden gotowy produkt zjeżdża z taśmy co kilka minut.
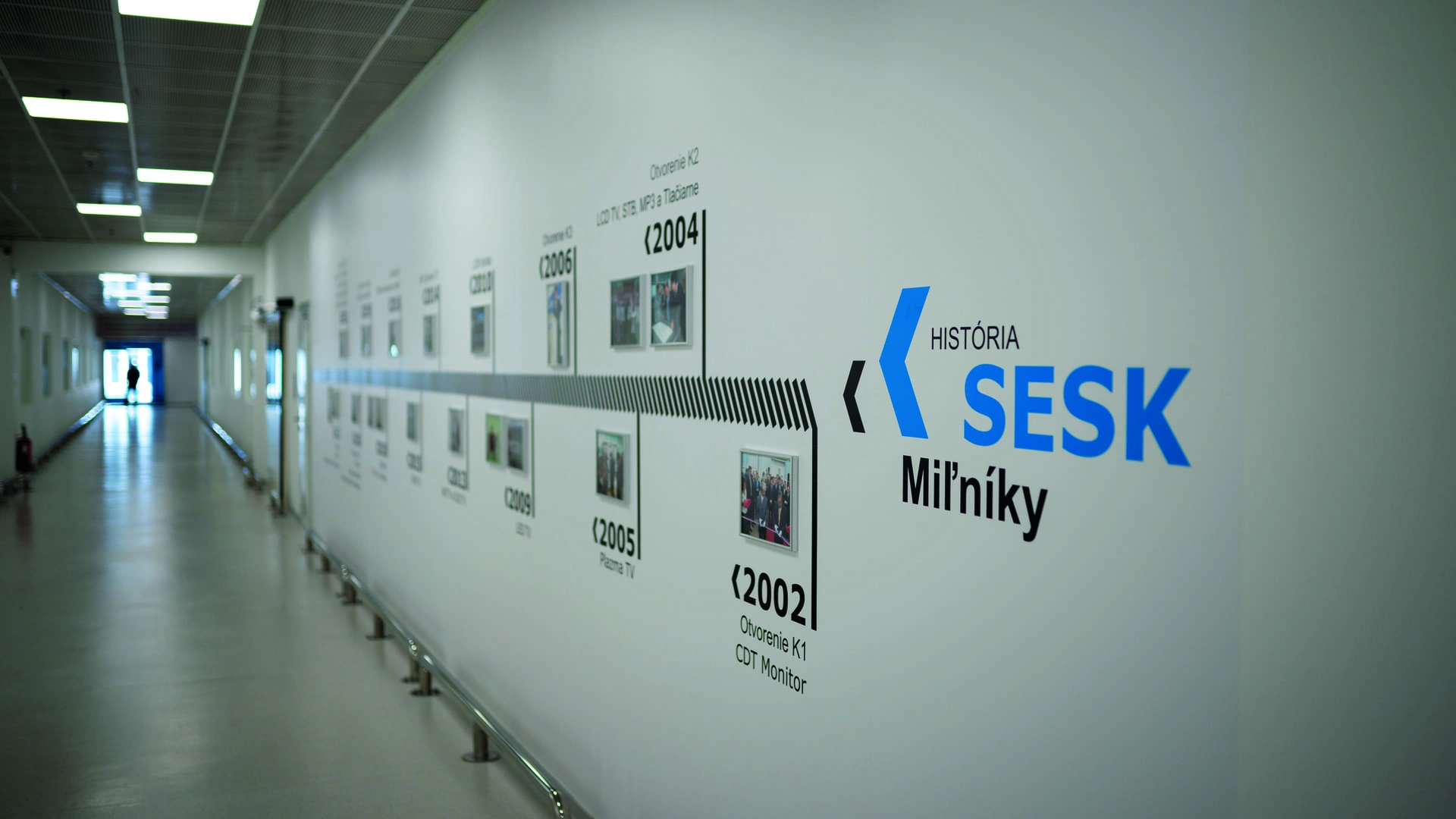
Niedaleko niej leży druga hala, która była celem mojej podróży. To właśnie tam powstają najnowocześniejsze i najdroższe ekrany, którymi może pochwalić się Samsung. Wykorzystują one technologię Micro LED, a za wartość urządzenia All in One złożonego z tych paneli można kupić sobie mieszkanie w każdym polskim mieście. Widziałem proces produkcji i jestem zachwycony, ale jednocześnie smutny.
Zanim jednak przejdę do właściwej części opowieści ze słowackiej fabryki, muszę podzielić się kilkoma spostrzeżeniami. Pierwszym z nich jest wszechobecność koreańskiego producenta w tym mieście. Jego logo zobaczymy na koszulkach lokalnego zespołu piłkarskiego, na billboardach czy na uczelni - wszędzie tam jest i wspiera działalność kulturalną, oświatową i społeczną. To nie ma żadnego wpływu na produkcję w fabryce, ale jakoś tak lepiej patrzy się na to, jak firmy próbują coś dawać, a nie tylko brać. Drugim jest obecność napisów pisanych cyrylicą w samej fabryce. Zdziwiło mnie to, ale powód ich obecności jest prosty - w fabryce znalazło zatrudnienie sporo emigrantów z ogarniętej wojną Ukrainy. Trzecim jest fakt, że fabryka wydaje się niepozorna, wręcz niewielka, gdy patrzy się na skalę produkcji.
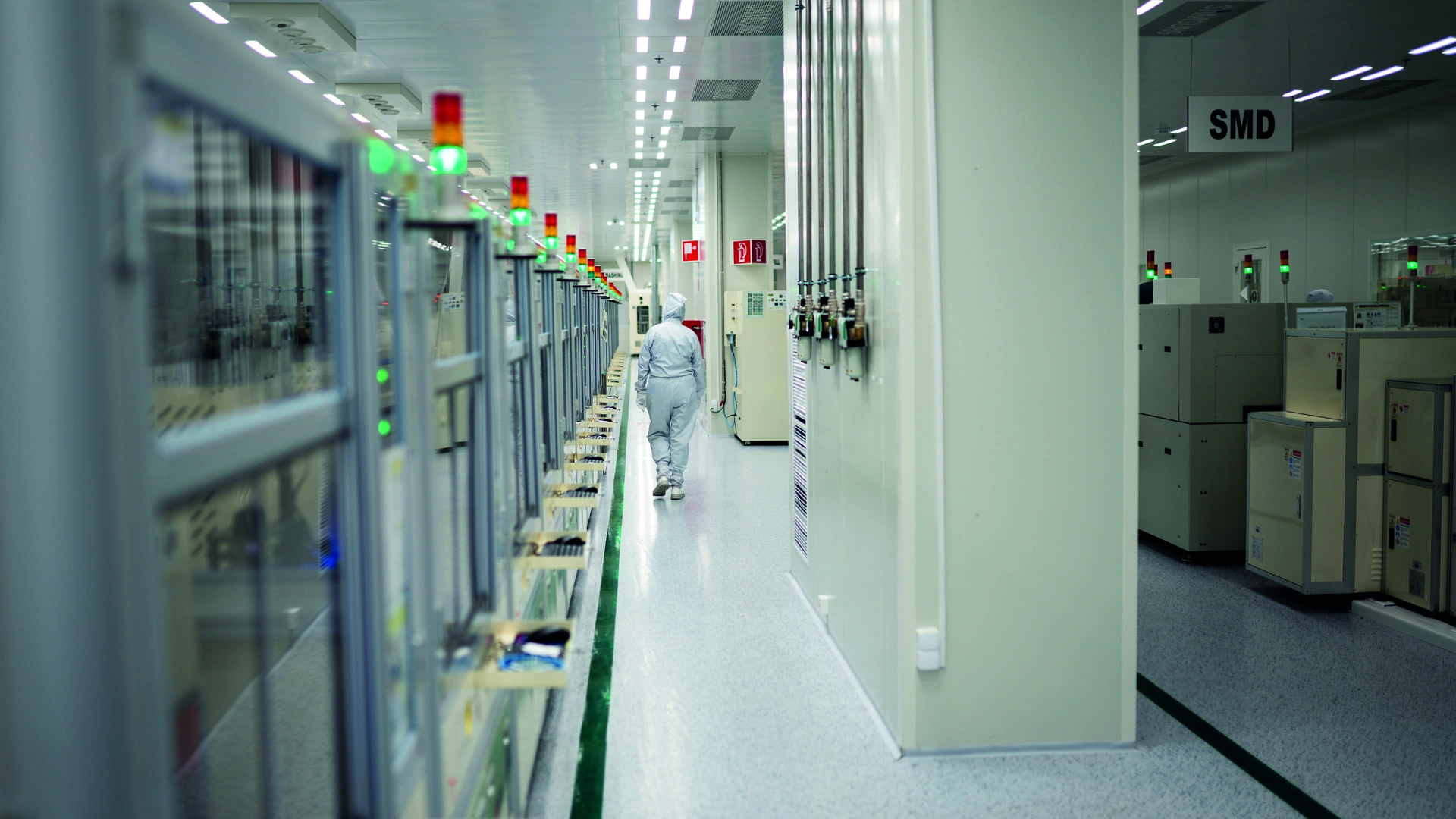
Jeszcze kwestia techniczna - w artykule nie znajdziecie wielu zdjęć, nie dowiecie się z niego nic na temat szczegółów technicznych procesu technologicznego, bo większość rzeczy, które widziałem objęta jest tajemnicą. Zaklejono nam aparaty w telefonach, a o części procesów nie informowano. Nie dziwię się, bo technologia jest warta miliardy, a szpiegostwo przemysłowe i biały wywiad mają się w najlepsze.
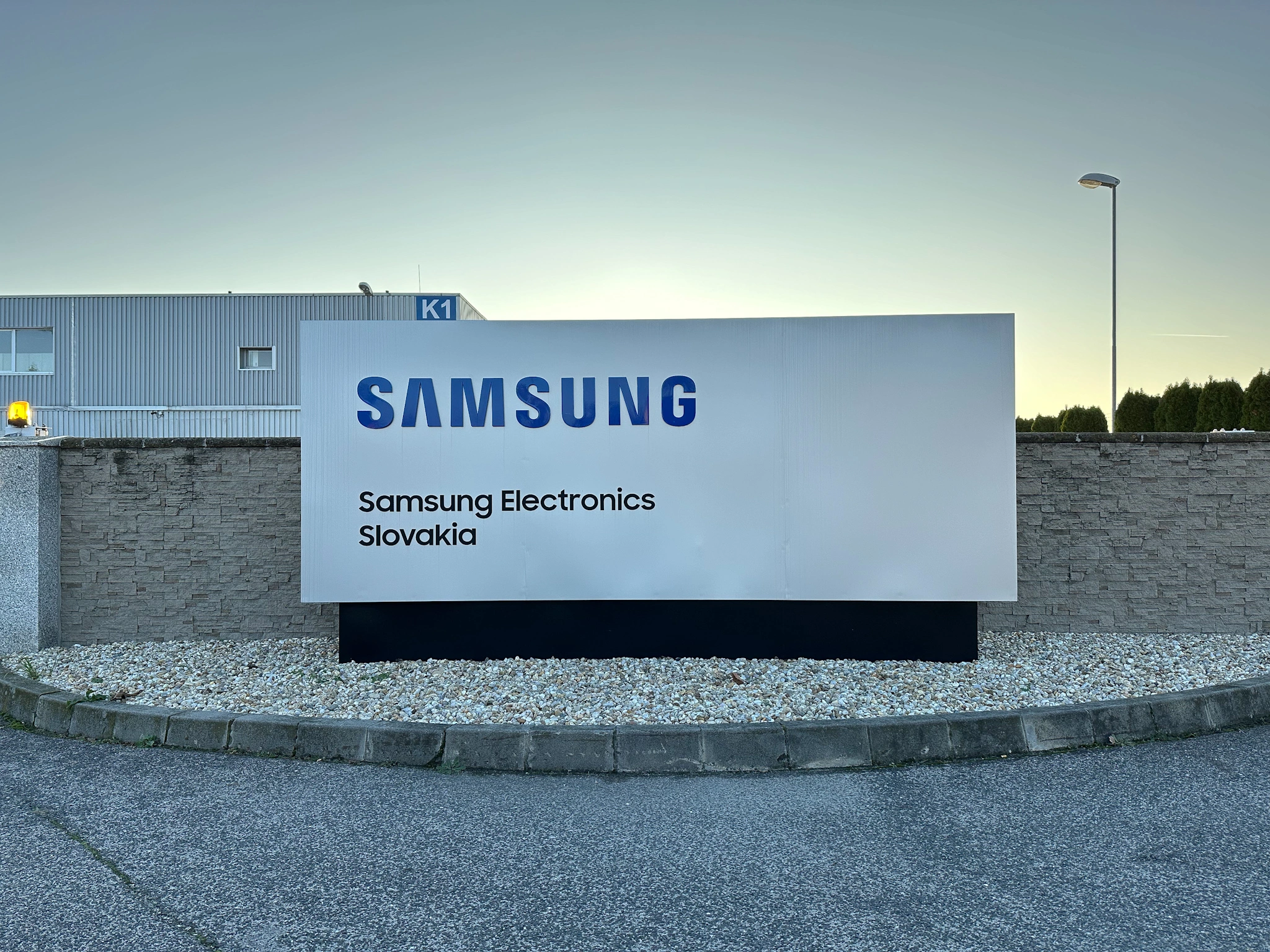
Micro LED - o co w tym chodzi?
Technologia Micro LED to szczyt rozwoju wyświetlaczy, dzięki której na zawsze zakończy się spór pomiędzy zwolennikami wyświetlaczy LCD a wyznawcami OLED-ów. Po prostu obie te technologie są przy Micro LED przestarzałe. W telegraficznym skrócie - matryce, które widziałem, wykorzystują samoemisyjne diody (tak jak wyświetlacze OLED), więc wyświetlane obrazy mają doskonały kontrast i reprodukcję ruchów. Diody są wykonane z materiałów syntetycznych (jak w matrycach LCD), a więc są bardzo trwałe i mogą operować ze znacznie większą jasnością i pokrywać szersze spektrum barwne. Jeden piksel to trzy diody ułożone obok siebie - niebieska, zielona i czerwona. W efekcie matryce Micro LED mają jakość obrazu jak w OLED-ach, a jasność wyższą niż LCD. To wyświetlacze idealne, na których ukazywane treści są tak dobre, że świat wokół ekranu wydaje się rozpikselowany i szary. Trudno to oddać zdjęciami i słowami, to po prostu trzeba zobaczyć. Jeżeli w waszej okolicy będą odbywać się duże targi Audio-Video, to możecie się na nie wybrać, bo istnieje duża szansa, że zobaczycie działanie ekranu na żywo. Alternatywnie możecie polecieć do Dubaju, do hotelu Atlantis The Royal, gdzie wręcz roi się od ekranów złożonych z paneli Micro LED.
W słowackiej fabryce powstają moduły, które używane są do tworzenia wielkich ekranów (takich jak na wspomnianym lotnisku) oraz urządzenia typu All-in-One, czyli składające się z modułów Micro LED.
Ekrany Micro LED nie potrzebują oddzielnego modułu podświetlającego i filtra kolorów. Sterowanie jasnością ma taki zakres, że nie ma drugiego takiego wyświetlacza. Niestety z racji tego, że jest to technologia przyszłości, to kosztuje majątek. W przypadku paneli Micro LED ceny zależą od wielkości i rozdzielczości ekranu, który się zamawia, a możliwości konfiguracyjne są nieskończone. Istnieją również modele All-in-One o określonej z góry wielkości: 110 cali (2K), 146 cali (2K) oraz 146 cali (4K). Ich ceny są płynne, zależą od rynku, ale można z powodzeniem założyć, że koszt najdroższego to okolice 200 tysięcy euro. Kosmos to mało powiedziane.
Oczywiście te ceny z czasem spadną, zwłaszcza gdy produkty The Wall trafią pod strzechy (a raczej bogate strzechy), ale nikt z nas nie zna planów Samsunga. Nawet na pytanie czy i kiedy planują wprowadzić do sprzedaży mniejsze rozmiary, przystępne dla ludzi, odpowiedź sprowadza się do enigmatycznego - taki jest cel, ale nie dowiecie się, ile jeszcze zajmie to czasu. Samsung technologię Micro LED pokazał już w 2018 roku i od tego czasu ciągle ją udoskonala. Z tej technologii wyspecjalizowały się już konkretne modele do określonej grupy docelowej, a producent stale poprawia parametry, które wydawały się nie do przeskoczenia. Stoi przed nim jeszcze kilka problemów wynikających z budowy paneli, złożoności produkcji i dostosowania jej do masowej skali, ale po tym co zobaczyłem żyję w nadziei, że za jakiś czas ekrany Micro LED trafią do naszych domów.
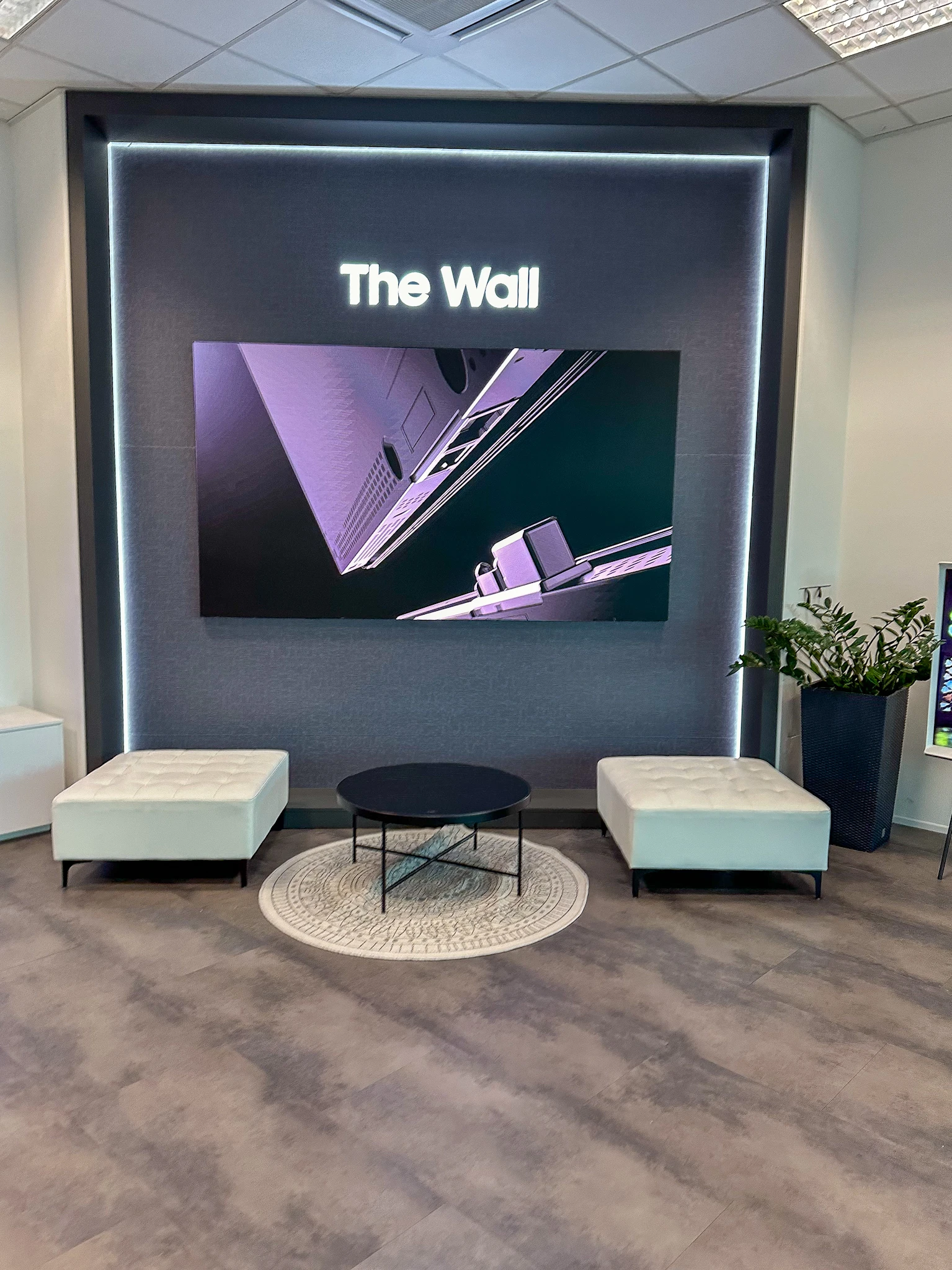
Fabryka jest sterylnie czysta
Przed wejściem musiałem ubrać się w kombinezon ochronny, założyć maseczkę i przejść przez śluzę powietrzną i dopiero moja stopa mogła stanąć na obszarze produkcji. Przeżyłem zdziwienie, bo myślałem, że będzie znacznie większy, tymczasem to niewielkie miejsce, które zostało podzielone na kilka stanowisk. Widziałem, jak wygląda proces montażu diod na czystym panelu. Fabryka produkuje trzy rodzaje paneli, które różnią się odległością pikseli od siebie (pixel pitch), co w konsekwencji ma wpływ na rozdzielczość i liczbę diod na jednym panelu, a także czasem produkcji jednego elementu. Klienci mogą wybrać odległość 1,26 mm (2K dla 110 cali), 1,68 mm (2K dla 146 cali) i 0,84 mm (4K dla 146 cali). Im mniej, tym lepiej, ale jednocześnie rośnie czas produkcji. Jeden panel ma wymiary około 20 cm x 15 cm i w wariancie 0,84 mm mieści ponad 120 000 diod Micro LED. Czas produkcji panelu wynosi od 5 do 9 godzin, co wynika z precyzyjności wykonania oraz tego, że producent przykłada ogromną wagę do kontroli jakości. Ciekawostką jest to, że diody LED nie są drukowane na płycie, tylko klejone, jedna po drugiej. Ramię maszyny, która to robi porusza się tak szybko, że wydaje się stać w miejscu.
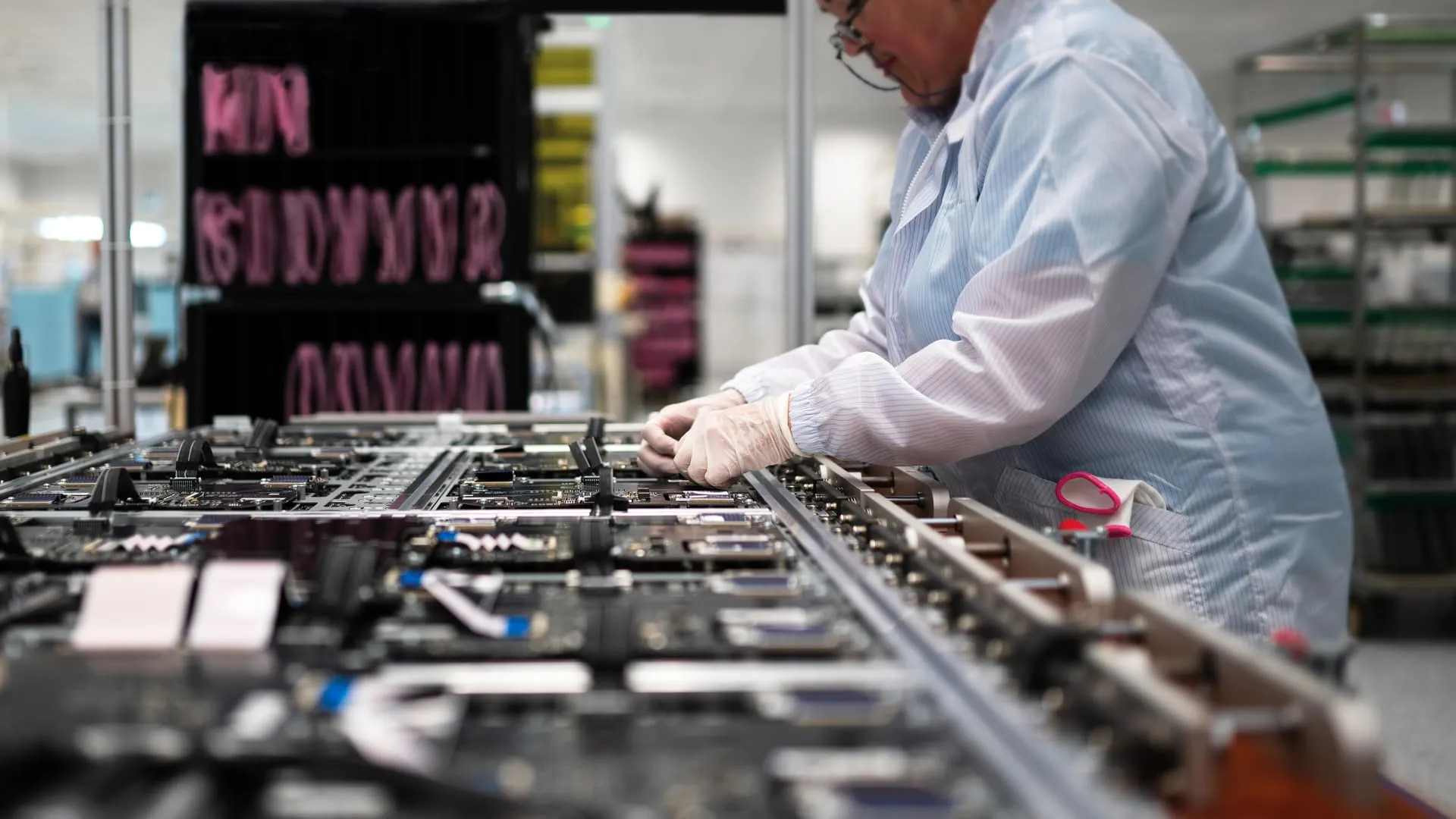
Sam proces powstawania jednego panelu podzielony jest na kilka etapów, a każdy z nich jest zakończony szczegółową kontrolą jakości. Zaczyna się przejawiać już na starcie produkcji, gdzie pracownicy sprawdzają jakość diod LED, które przyjechały do fabryki. Technologia produkcji pozwala na wyłapanie usterek, np. źle zamontowanej diody LED i jej poprawienie. Dzięki temu, że każdy etap zakończony jest kontrolą jakości, to pracownicy dokładnie wiedzą, kiedy wystąpił defekt. Tajemnicą poliszynela jest to, że im później wystąpi, tym bardziej skomplikowane jest jego usunięcie. Na początkowym etapie trwa to dosłownie chwilę, a na końcowym sprawia, że trzeba powtórzyć większość procesów, co wiąże się z czasem, kosztami i ryzykiem niepowodzenia. Ten technologiczny reżim powoduje, że finalnie Samsung szczyci się maksymalnie 1 proc. możliwych defektów, czyli na 192 panele potrzebne do wyprodukowania całego urządzenia o przekątnej 146 cali, dwa z nich mogą być wadliwe. Za takie uważane są np. te, w których 2 diody niebieskie nie świecą, albo 2 czerwone. Natomiast jeżeli nie świeci dioda zielona, to panel z miejsca uznawany jest za wadliwy. Powtórzę 2 ze 129 tysięcy.
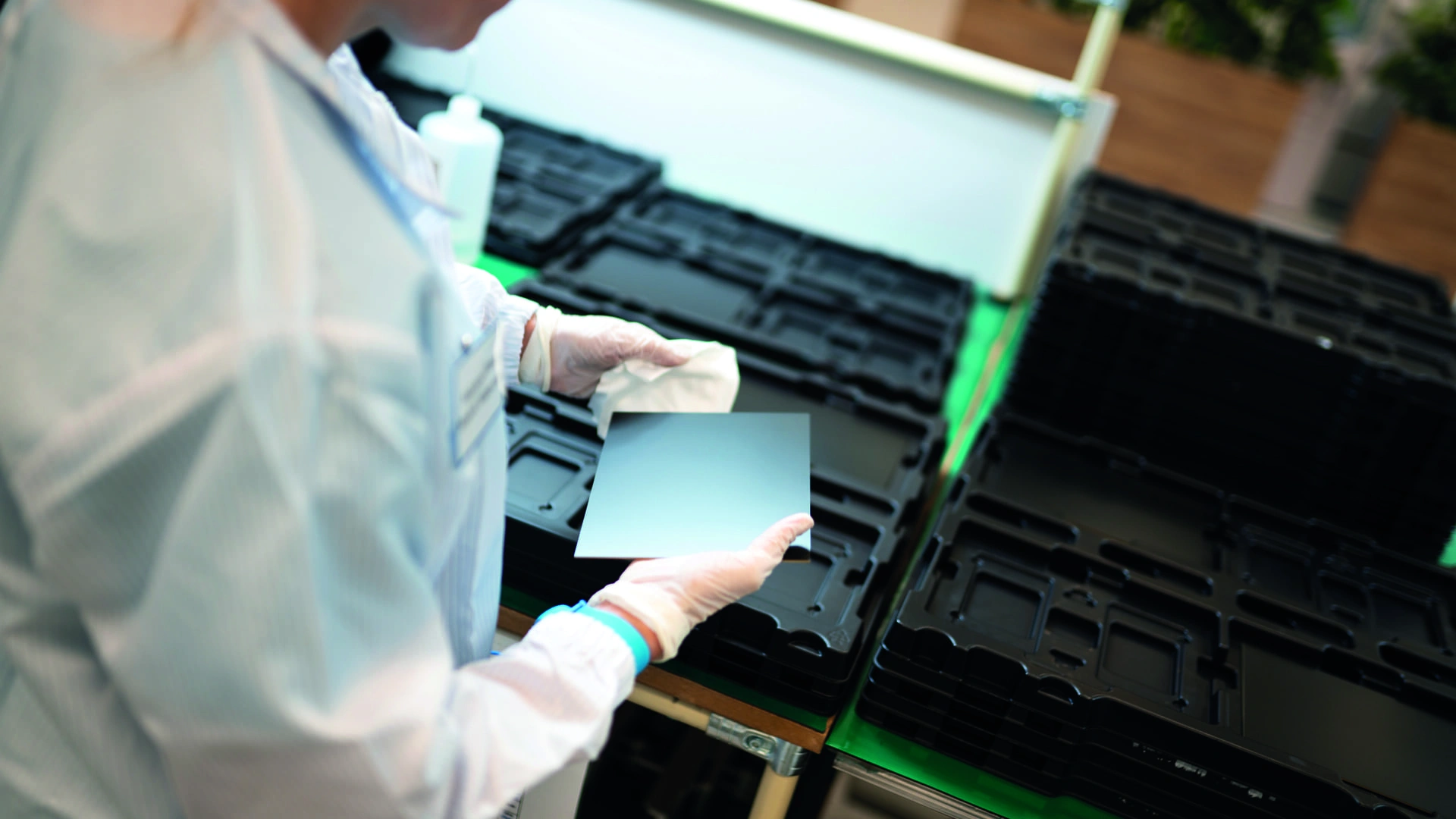
Zdziwiłem się, że pomimo automatyzacji wiele czynności wykonują ludzie, zwłaszcza tych związanych z kontrolą jakości. Kamera nie jest w stanie wyłapać pewnych defektów, które od razu zauważają ludzie, np. załamanie światła, nierówności, odrobinę mniejsza jasność diody. To też jest jednym z powodów długotrwałości procesu produkcji paneli. Z drugiej strony jeżeli płacisz ciężarówkę pieniędzy, to oczekujesz najwyższej jakości i to właśnie dostajesz, jeżeli kupisz ekran Micro LED z serii Samsung The Wall.
Po tym jak panele są ze sobą połączone następuje seria testów, w tym jeden polegający na 72-godzinnym włączeniu paneli i sprawdzeniu wszystkich funkcji. Po nim następuje ostateczna kalibracja i moduły mogą trafić do pudełka, a stamtąd do klienta.
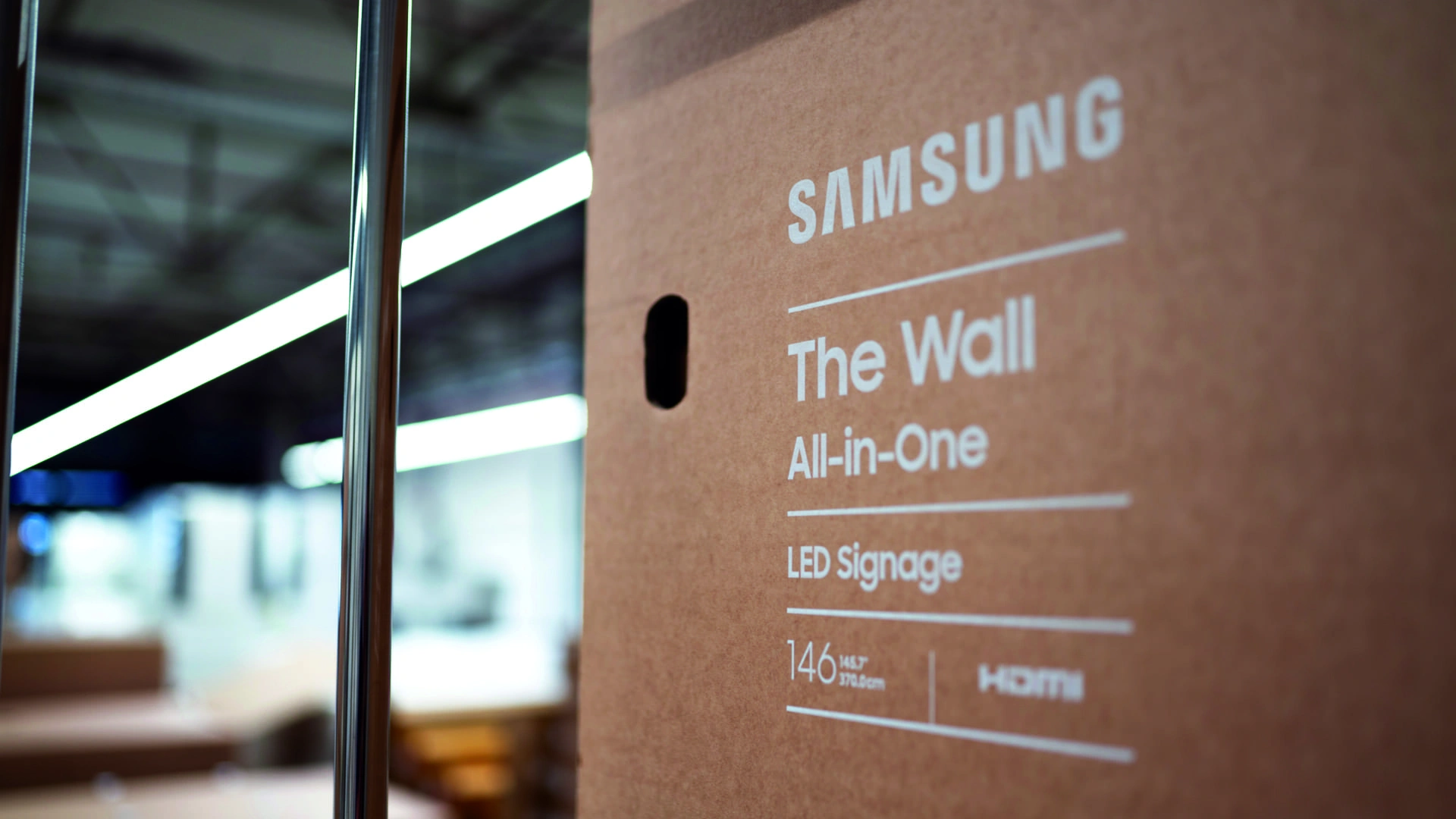
Samsung wielokrotnie powtarzał, że najważniejsi są ludzie i to widać podczas wizyty w fabryce. To ludzie sprawdzają, czy maszyny dobrze wykonały swoją pracę oraz skręcają i dopasowują panele do siebie - ludzka ręka jest w stanie wykryć nierówności i odpowiednio je zniwelować, a dla automatycznego ramienia byłoby to już zbyt skomplikowane zadanie. Taki proces produkcji jest wolny, ale jednocześnie znacznie dokładniejszy. Zapytałem o to, czy nie mają problemów z tak rozciągniętym w czasie procesem produkcji, ale okazało się, że produkują z kilkutygodniowym wyprzedzeniem, więc nie ma mowy o żadnych opóźnieniach. Moce produkcyjne pozwalają na wyprodukowanie czterech urządzeń All-in-One i 40 modułów (kilka połączonych ze sobą paneli) na jednej 8-godzinnej zmianie.
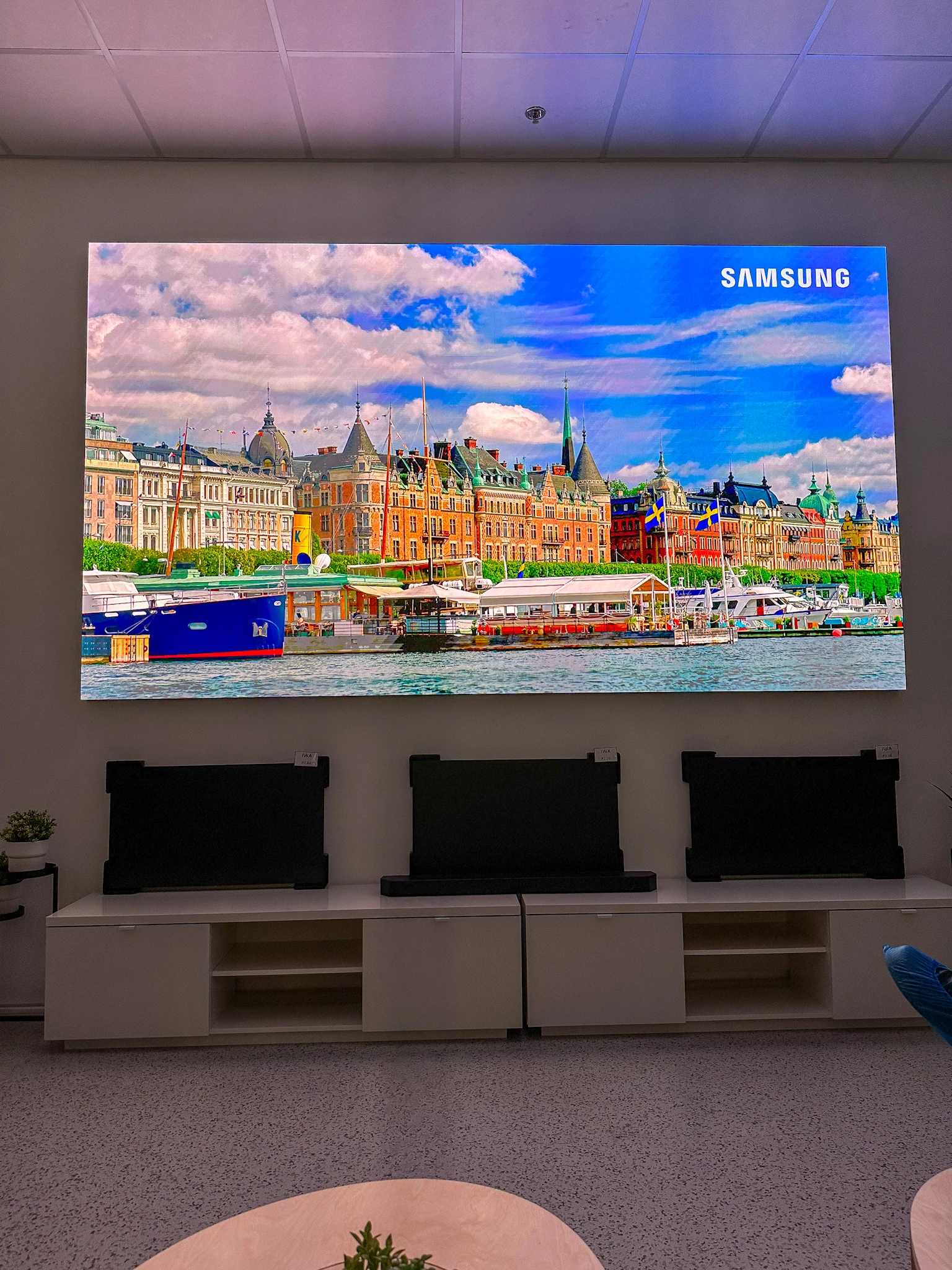
Samsung The Wall (All in One) złożony z paneli Micro LED - budowa
Samsung The Wall (All in One) w rozmiarze 146 cali składa się ze 192 paneli połączonych w jedną całość. W oczy rzuca się absolutny brak ramek - urządzenie kończy się tam, gdzie znajduje się linia wyznaczona przez skrajne piksele. Jeżeli chodzi o łączenia to z bliska są one widoczne, a także wtedy gdy wiemy, gdzie ich szukać w bardzo jasnych ujęciach. Jednak po zajęciu miejsca na kanapie w prawidłowej odległości od ekranu w zupełności nie przeszkadzają. A z czasem przestaje się je zauważać.
Do użytkownika urządzenie przyjeżdża w formie 4 modułów (każdy po 48 paneli), które trzeba ze sobą połączyć za pomocą specjalnej metalowej ramki. Ciekawostką jest to, że proces produkcji i starzenia paneli sprawia, że nie można dowolnie wymieniać paneli, ani dokładać nowych, bo będzie wtedy widoczna różnica w jasności ekranu. TV składający się z czterech modułów jest kalibrowany przed włożeniem do pudełka. Zadacie sobie pytanie, a co jeżeli coś się popsuje? Szanse są na to minimalne, bo diody Micro LED mają naprawdę wyjątkową żywotność, około 150 tysięcy godzin ciągłego świecenia, czyli około 17 lat. Ale jeżeli do tego dojdzie to Samsung ma ciekawą praktykę - tworzy kilka modułów na zapas, które są przypisane do danego zamówienia i przechowywane przez okres 10 lat.
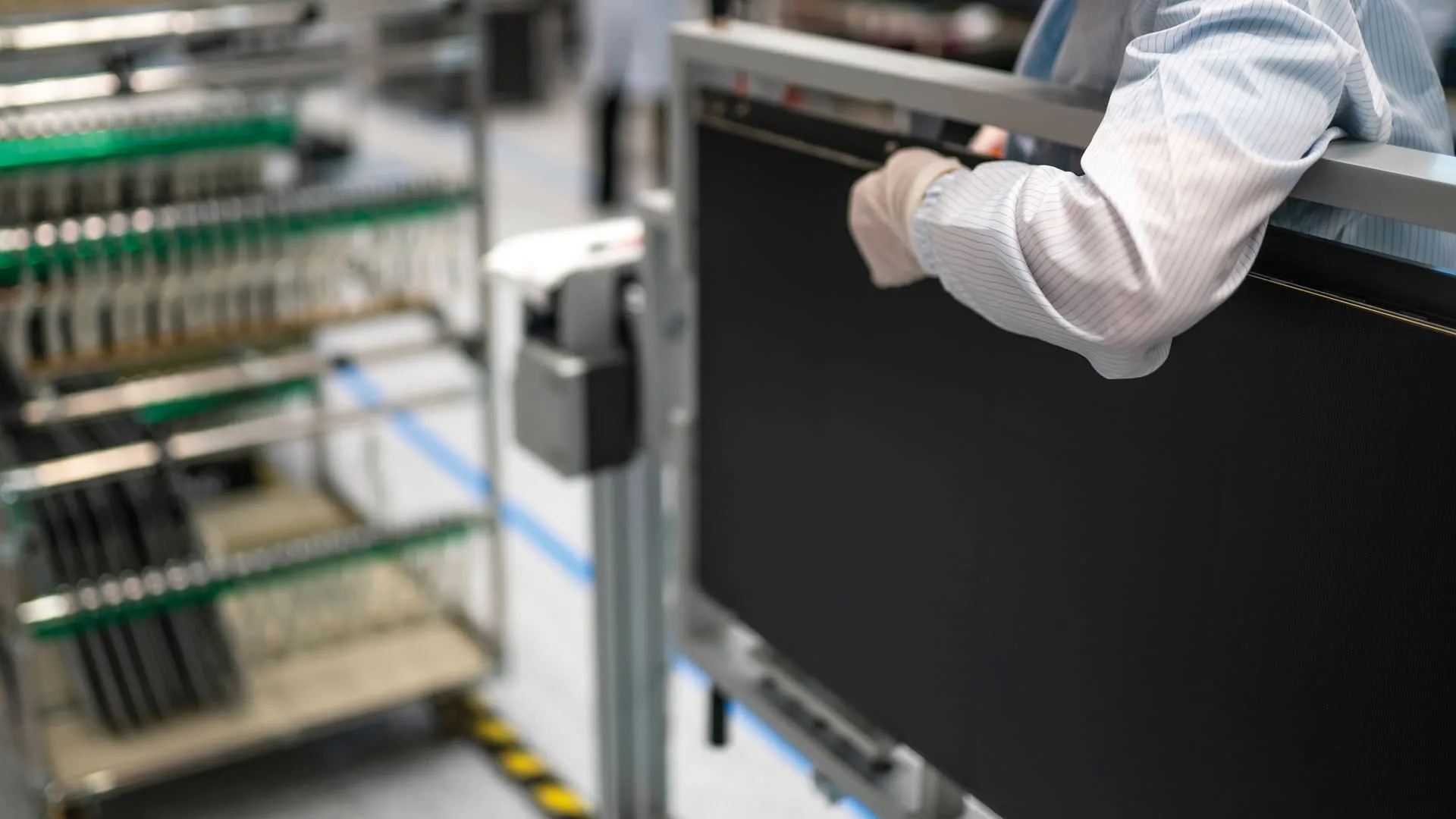
4 moduły połączone ze sobą tworzą działające urządzenie, nie ma tutaj żadnych kabli, tylko wpina się jeden moduł w drugi. Użytkownik wybiera jaką wersję oprogramowania chce - profesjonalną, która powstała z myślą o salach konferencyjnych oraz użytkową, czyli dobrze znany Tizen. Jeżeli fundusze wam pozwalają, to nic nie stoi na przeszkodzie, żeby podłączyć do TV konsolę i grać w 146 calach. Ciekawostką jest to, że moduł One Connect umożliwia jednoczesne podłączenie 4 kabli HDMI i jest w stanie wyświetlić obraz z czterech źródeł jednocześnie - dzieląc ekran po równo, albo z jednym ekranem dominującym.
Spodobał mi się proces produkcji paneli Micro LED, który pokazał mi Samsung
W swoich materiałach producent często używa pojęcia, że produkcja modułów Micro LED to rzemiosło i jestem w stanie się z tym zgodzić. To idealne połączenie nowych technologii i ludzkich możliwości. Nie ma tu jeszcze miejsca na bezduszne maszyny, ale to odbija się na cenie. Stoję na stanowisku, że Samsung powinien zabierać do fabryki każdego kupującego panele Micro LED, żeby miał świadomość dobrze wydanych pieniędzy.